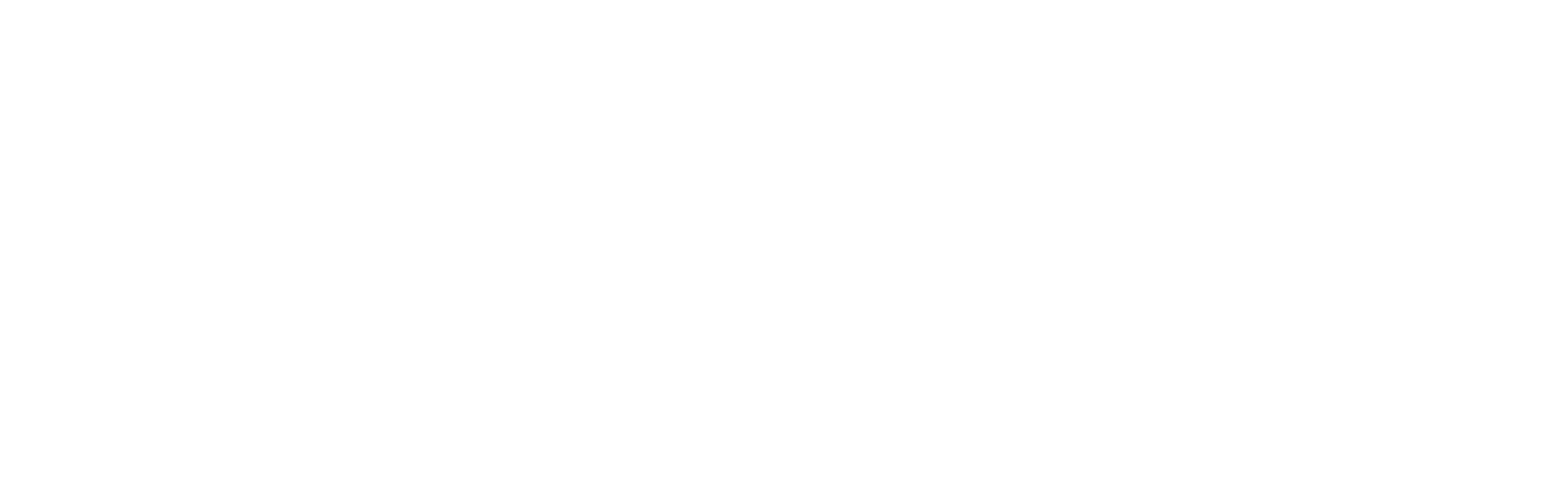
When selecting your next temperature monitoring system for your mass concrete application, its important to know the benefits and disadvantages.
When selecting your next temperature monitoring system for your mass concrete application, the first criteria to look at would be the hardware. Does the sensor have the required accuracy? How will the data be collected? How deep can it measure temperature in the element? The temperature measurement systems for concrete that are currently available in the market are categorized as:
a) Thermocouples
b) Wired temperature and maturity loggers
c) Wired concrete sensors with external wireless transmitter
d) Fully embedded wireless concrete sensors
Each of these temperature monitoring systems has their advantages and disadvantages.
It is important for project managers to review these before developing their thermal control plan in a bid to ensure adequate quality control and, ultimately, to maximize their return on investment (ROI)
A concrete thermocouple consists of two wires of different metals twisted together at one end to form an electrical junction. There is a temperature-dependent voltage that is produced by the thermocouple due to its thermoelectric property. This voltage is measured by external equipment and is then used to estimate the concrete temperature. The base metal thermocouple type J and K are the most commonly used type of thermocouples in the concrete industry as they are relatively inexpensive (about $1/ft) with a wide range of temperature measurements. At one end, the two thermocouple metal wires need to be twisted together and at the other end the two wires are connected to a measuring unit. The wires need to be labelled for identification and stay connected to the external device throughout the monitoring period, until the measurement duration is completed. The individual measurements are typically displayed on the unit. Once the measurements are completed, the unit can be connected to a computer to download and analyse the data. Recently, wireless devices have been introduced that send the thermocouple measurements to the cloud or a smartphone. Although thermocouples are relatively inexpensive, they have several disadvantages that make them not suitable for use in most concrete thermal control plans.
1.) The measurement accuracy of thermocouples is relatively low. Type J and K thermocouples have a standard error limit of at least 4°F (2.2°C) for typical concrete temperature ranges. This error is more than two times higher than the minimum measurement accuracy required in most concrete temperature measurement specifications.
2.) Setting up this system is very time consuming; to cut the wires, attach them to the plug, and install in the field.
3.) Thin thermocouple wires are very prone to internal cuts and damages, and therefore measurement errors as they are typically not designed for harsh construction environments.
4.) The wires coming out of the concrete and the external unit need to be protected throughout the entire temperature measurement period. Even at a low price, the disadvantages associated with thermocouples don’t make this temperature monitoring system ideal for mass concrete applications as the installation becomes very time consuming and can be complex in certain cases because of the size of certain mass elements. More importantly, it doesn’t provide the accuracy required for measuring maximum concrete temperatures and temperature differentials, which is critical for this type of application.
To address some of the challenges in thermocouple-based systems, wired temperature and maturity loggers were developed. These loggers and meters have an electronic circuit board that contains a coin-size battery with an onboard thermistor for temperature measurement. The measurements are recorded and stored on this circuit board at pre-defined intervals. For the installation of these systems in concrete elements, the logger (or the sealed circuit board) is placed at the location where the temperature measurements need to be recorded in the mass element. The connector wires are left out of the structural element. As the concrete ages, users can connect their hand-held unit to the end of the wires to download the recorded temperature values. The wires used for these types of temperature/maturity loggers are more rugged compared to thermocouples which makes them less prone to damage on the jobsite. The external unit is in a constricted environment and therefore not exposed to potential damage as it is used only when downloading the data. External devices can offer various types of data analysis in the field. For full analysis and report generation, the data needs to be downloaded to a computer.
Some of the disadvantages of this set up include:
1.) Like thermocouples, the ends of the wires need to be labelled for identification after pouring and must be protected against potential cuts or other damages on the jobsite.
2.) These types of temperature loggers do not have an electrical switch and are always turned on, so their shelf-life is limited.
3.) The industrial-grade connector cable makes these sensors bulky and difficult to install, especially when long wires are used for large structural elements.
4.) Finding the cable lead during the first few days after pouring could be challenging as there are many construction tools, materials and components being moved and displaced on the jobsite, potentially covering the cable lead.
5.) The ends can get cut or buried in concrete during or after placement.
6.) Some systems require a data logger constantly connected to the thermocouples.
Typically, people tend to bundle the wires at the same location for ease-of-use which requires longer wires. This system can become quite cumbersome with wires sticking out everywhere in large concrete elements. Additionally, manual analysis and reporting is very time consuming.
Whether you are using thermocouples or wired loggers for concrete temperature monitoring, the hassle of connecting to an external device and the need to visit the jobsite to collect the data and later download it to a computer have prevented these types of sensors from wide industry adoption. With electronic advancements, wireless data transmitters were developed to address the above challenges. These external units are connected to the end of the wires coming out of concrete to store and transfer the temperature measurements over a wireless network:
- To a computer connected to the internet
- To a local wireless hub or gateway that then transfers data to cloud
- Directly to cloud through networks such as LTE or Sigfox.
In this system, the wire connection to the external unit is still prone to cuts and the wireless unit located close to the concrete placement can be damaged in a harsh construction environment. Moreover, a complex system comprising wires, external transmitters, and local hubs can be challenging to install and configure as it has several different components. In a mass concrete element, the surface often needs to be protected and insulated in order to prevent a large thermal gradient. Temperature monitoring systems need to be installed in such a way that they do not obstruct blankets or insolation systems. Furthermore, in remote jobsites where cell network connection is not available or if any of their components are damaged, these systems may not function properly. In some locations, power is also not easily accessible which can make it hard to provide consistent power to some hubs or gateways. Despite some of the disadvantages, these systems have been successfully used in mass concrete placements over the years. A great advantage of these wireless systems is that the data analysis can be done automatically on the cloud to generate custom alerts and notifications for project managers and superintendents even when they are not on the jobsite. Mass elements typically require at least 2measurements at each location, one for the core and one for the surface, sometimes more. To reduce the number of transmitters some systems have the capability to receive more than one wire connection, making data collection and analysis faster and easier.
With the advancements in electronics and wireless technologies, self-contained wireless concrete sensors and loggers that are fully embedded in the concrete have been created. The temperature measurements are stored on the sensor. The recorded data can then be downloaded from the fully embedded sensor through various wireless communication protocols such as Bluetooth LE, LoRa, Zigbeeor Wi-Fi. In the case of Bluetooth LE, a smartphone or tablet can be used to connect wirelessly to the sensor to download the data and analyse it in real-time for maturity and strength estimation using mobile apps. The data is also transmitted to the cloud using the mobile device’s connection to the cell network. Alternatively, the sensor data can be downloaded automatically using a wireless local hub for transmission to the cloud without the need to visit the jobsite. The main advantage of fully embedded wireless concrete sensors is that, unlike wired systems, they are not prone to potential damage on the construction jobsite after pouring. The data is securely held on the sensor inside the concrete and can be conveniently downloaded at any time. The installation and data collection are relatively simpler and faster as there are no wires to be dragged outside of the mass concrete element, or in the case of Bluetooth, no external units that need to be maintained. It should be noted that the wireless signal from these sensors can only go through a couple inches of concrete. So, for deeper locations, a temperature measurement cable is used while the wireless sensor’s transmitter is placed inside the concrete typically on the rebar below the concrete surface. Mass concrete projects, such as windfarms, dams or some large civil projects can often be located at remote sites or sometime underground. The wireless system always provides a connection solution that is not dependent on LTE which makes monitoring accessible in every location. For mass concrete applications this system becomes very easy to use and less cumbersome. Some systems additionally offer more than a single point of measurement which means the surface and core can be simultaneously monitored with the use of only one sensor, reducing the overall number of sensors required for the project. Data analysis such as temperature differentials can be done automatically on the phone or the cloud while providing the same advantages as the previous system. The biggest limitation for a mass concrete element would be the range between the phone/hub and the embedded sensor where careful consideration might be taken in terms of placement of the hub or gateway for remote monitoring options, or the potential difficulty in accessing a connection with a cellphone.
For the full eBook you can request a downloadable PDF here
We won't bombard you with emails. Stay updated with industry news and new products.